Dry Lubrication for Can, PET, Carton, Keg and Glass Bottle Lines on Plastic and Stainless Steel Belts
DryFormance™ combines water-free conveyor lubrication technology with packaging line engineering excellence to deliver against water reduction and health and safety targets as well as improving your overall operational efficiency and helping you to meet your sustainability commitments.
We provide an engineering solution to one of the most important yet misunderstood parts of running an efficient packaging operation by combining:
- Water-free, PTFE-free and silicone-free lubricant
- Optimised zonal distribution and volume control method
- Unique brush and insert application method
- Engineering expertise and service maintenance
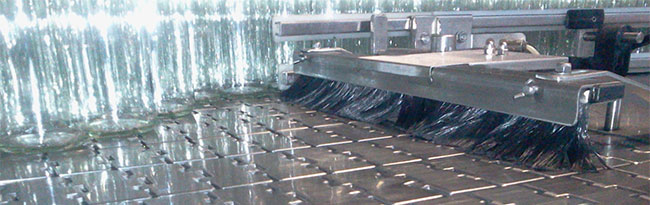
DryFormance Lubricant
Formulated specifically for use with plastic or stainless steel conveyor belts, DryFormance lubricants require zero water in the lubricating process and do not add any load to effluent. They are NSF H1 approved for incidental food contact and safe for use on inverted cans.
Zonal Distribution System
When designing your bespoke system, we section the full packaging line into smaller zones determined by characteristics specific to that zone such as conveyor speed, package weight, number of packages, single track section, mass accumulation etc. As a result, lubricant dosage is optimized, enabling coefficient of friction to be controlled to ensure package stability with zero excess lubricant ending up on the packaging hall floor.
Our system is responsive to run signals making sure that static conveyors are not being lubricated.
Application Method
Lubricant is secreted onto a soft, bristle brush causing the bristles to become coated in lube. This allows for an even distribution of lubricant across the entire conveyor belt and no excess ending up on the floor. Our brush assembly is designed with ease of servicing in mind.
Lubrication is also applied to the underside of the belt using application inserts. This reduces the coefficient of friction between the conveyor belt and the wear strip, reducing wear and tear of the belt. Additionally, it reduces the load on motors 'pulling' conveyors along which are weighed down with filled containers. This reduces motor energy usage, carbon emissions and motor trips which could lead to an unplanned shut-down.
Service and Knowledge
We work with on-site technical teams to ensure a smooth installation and commissioning program that fits in with existing production schedules and minimises disruption. Once up and running, your system is maintained by our experienced team of solutions providers who perform essential operating maintenance, such as replenishing lubricant volumes, measuring the coefficient of friction and adjusting dosage volumes. During their visits, they monitor product traffic behaviour and production performance as a method of preventative maintenance, but in many instances prove to be an extra pair of eyes on large sections of conveyorage which are regularly unmanned as a result of resource engineering pressures.
Using their packaging line knowledge gained from working across a wide range of food and beverage customers they will feedback advice on areas for improvement and optimization, keeping your site at the forefront of manufacturing excellence.
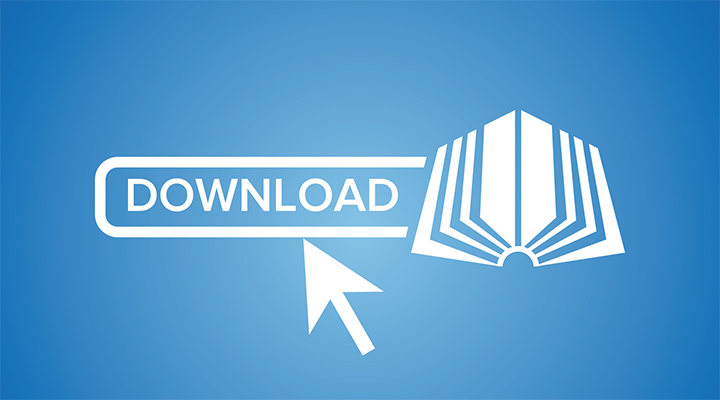